Lean and Six Sigma Training
- Home
- Lean and Six Sigma Training
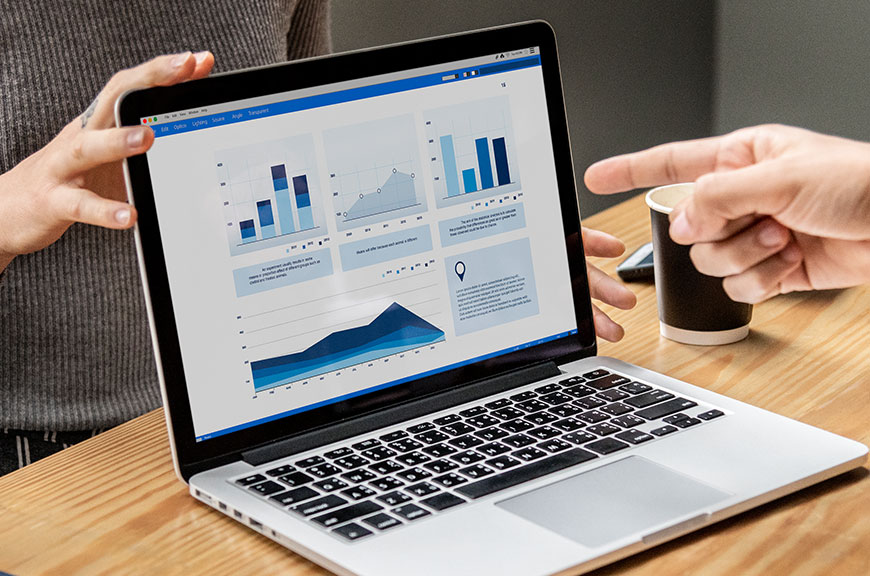
Master Lean and Six Sigma to Drive Operational Excellence
At CMSL, we offer comprehensive Lean and Six Sigma training programs designed to help businesses streamline operations, improve quality, and increase profitability. Whether you’re new to Lean and Six Sigma or looking to enhance your existing skills, our training equips your team with the tools and techniques needed to eliminate waste, reduce variability, and achieve sustainable improvements.
Services
Contacts
Visit Our Offices
Green Leaves Complex, along Lake Drive, Next to Luzira SS. Luzira - Kampala, Uganda.
Have Any Questions?
0704 343 780 | 0783915 989
0700860 506 | 0775 630 989
Mail Us
info@crosslinemsl.com
Our Lean and Six Sigma Training Programs
Lean Training
Learn to eliminate waste and improve process flow with Lean principles.
- Introduction to Lean Principles: Understand the core concepts of Lean, including value stream mapping, 5S, and Kaizen.
- Waste Elimination: Learn to identify and reduce the seven types of waste in your processes (Overproduction, Waiting, Transport, Extra Processing, Inventory, Motion, Defects).
- Process Improvement Techniques: Master tools like Value Stream Mapping, 5S, and Kanban to streamline operations.
- Continuous Improvement: Foster a culture of Kaizen by training employees to continuously identify and implement improvements.
Six Sigma Training
Achieve high levels of quality and process improvement with Six Sigma methodologies.
- Introduction to Six Sigma: Learn the fundamentals of Six Sigma, including the DMAIC (Define, Measure, Analyze, Improve, Control) framework.
- Data-Driven Decision Making: Develop skills in statistical analysis, process control, and hypothesis testing.
- Root Cause Analysis: Use tools like Fishbone Diagrams and Pareto Charts to identify and address the root causes of problems.
- Project Management: Learn how to manage Six Sigma projects effectively to deliver measurable improvements.